Progress: Hulls Kiss the Water – Oh Oh!
- Blue Tortuga
- Jul 15, 2023
- 4 min read
After the long trek through the dark to arrive at the marina, we were scheduled for 7 AM launch; the first of the day. We were tired, but excited. The mast manufacturer, Sparcraft, was already lined up outside the launch area. We learned the crane would place the vessel in the water, Sparcraft would step the mast (which is the process of using the crane to place the mast on the vessel) and secure the standing rigging. Then the vessel would be moved to a slip and the sails would be added by NorthSails. It would be a very busy day! But the best laid plans do not always go as intended. . .
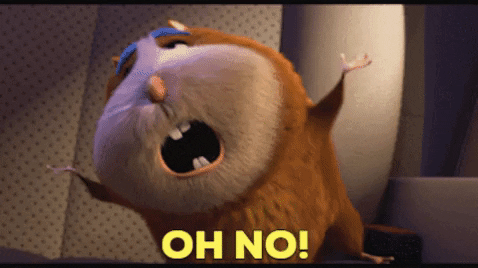
It is easy to forget, in the midst of all that needed to be done, that Blue Tortuga was in such an iconic place – Royal Cape Yacht Club. Located at the base of Table Mountain in Cape Town, South Africa – some incredible pictures captured the launch for posterity.

The owner of Celtic Yachts provided a bottle of champagne to toast the launch and christen Blue Tortuga. We appreciate Elliot, the marina manager with the Royal Cape Yacht Club, allowing us to take the time to toast the achievement and relish in the moment, even it it was only for a moment or two.
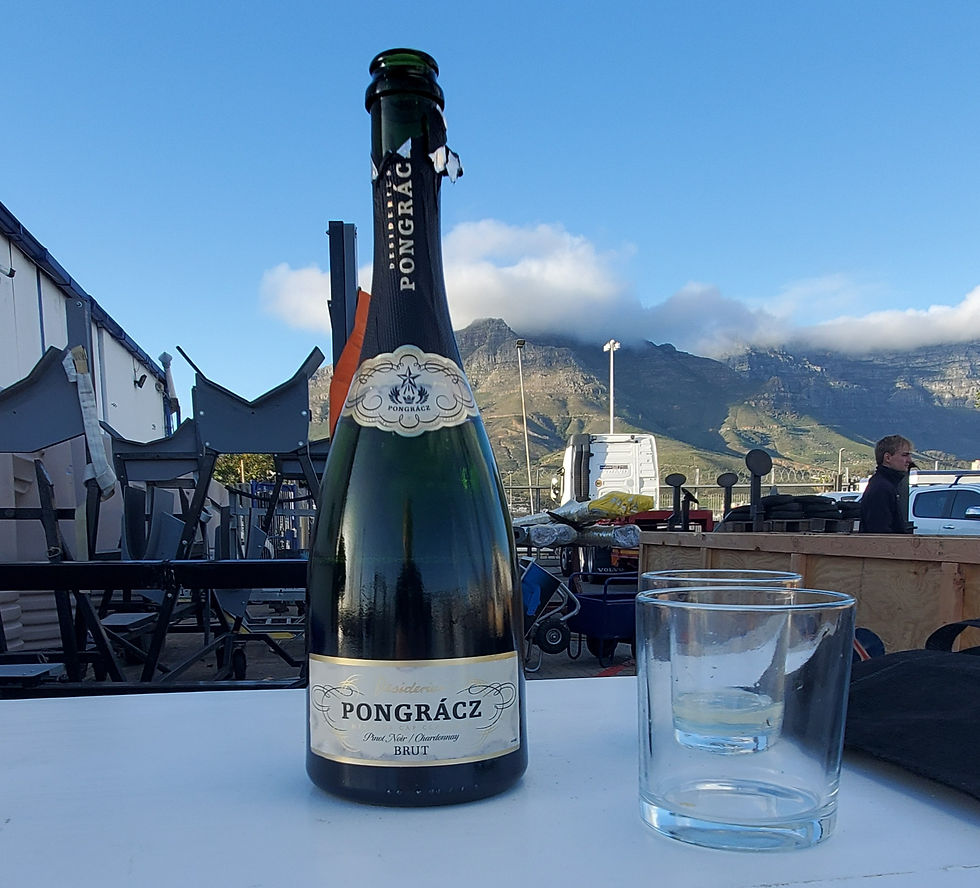
The Royal Cape marina workers moved like well-oiled machines expeditiously moving the boat from the truck, spinning her around, and moving to a place where she touched the water for the first time. As her keels are lowered into the water and the hulls come to float the weight of the 18,000-pound vessel, the Celtic Yachts team moved down the dock to step onboard and check things out.
To our dismay, the team quickly disembarked from the vessel and the crane moved to put Blue Tortuga back on the dock. From the look on their faces there was something very wrong. The builder was embarrassed, the operations manager angry, the lead supervisor clearly uncomfortable . . . as it came to light that the thru hulls were leaking. Not just one or two, but ALL the thru hulls. In front of all the on-lookers, larger boat manufacturers, workers, and visitors to the Royal Cape, the Celtic Yachts team held up the launch schedule for the day while they replaced two of the worst leaking thru hulls for all to see. While the embarrassment was clear, stories of other bungled launches, by other manufacturers, quickly became the talk of the marina. This only added to our concerns regarding whether the Admiral 40 was being built by people that had any idea what they were doing.
We learned that a separate haul out was scheduled (at the builder’s expense) early next week to replace all the remaining thru hulls. Some out of prudence, some out of liability fears, some because the leaks were slower, the embarrassment was not over for Celtic Yachts.
In the meantime, work to finish the boat continued – and we were glad the work continued as the boat was missing significant components to be able to leave the dock including floors, 110v outlets, 12 v outlets, plumbing drains and showers, cabinet doors, LP gas, Bimini panel seals, and of course, the never-ending gelcoat work. In fact, the vessel did not have a single working toilet when the boat launched, or hot water.
With so much work to be done, it is a wonder that we launched. But remember, our visa extension was to expire the next day and the build was already 4 months behind schedule. Our biggest mistake was trusting the builder when he told us the build was running on schedule in late September when we made the irreversable decision to ship our crate to South Africa. Somewhere between September 20th and November 8th when we got the call about the delay, Tim Duncan, the owner of Celtic Yachts realized that the boat would not be completed for the December 1st launch date.
The big question
How is it that less than 30 days from the scheduled launch Tim Duncan doesn’t recognize that the build is so far behind schedule that four months later they are STILL not finished? And how much longer would it take? A month? 6 months?
For us, the shipment of our crate to South Africa was a significant commitment. Let me explain:
The crate had to be received to the ‘launched’ vessel. If the vessel was not ready the crate would end up in ‘bonded-custom storage’. The fees were approximately 3,000 Rand ($160 US) each month, not to mention the potential for rats, bugs, and theft.
2. Once the crate was received to the vessel, the contents needed to leave the country in 90 days or import tax would be due for the value of the crate contents.
In order to get back to the US, we needed to leave South Africa with enough time to sail to Cape Hatteras before July 1st. This location and timing were decided by our insurance company. If we were unable to make those deadlines there would be no coverage for the vessel due to hurricane season.
We had contracted with and paid a captain to sail with us across the South Atlantic. We were working with his schedule as well. He had another delivery to complete in approximately mid-June. (He informed us he had already missed the test sail and commissioning and that owner was anxious to get the vessel to the final destination – Straits of Gibraltar.)
We had been paying for an apartment for the months following the delay.
Our visa clearly would expire before we could get the vessel our of the country – how much trouble would we be in trying to leave the country? It was anybody’s guess.
Our boat contract had a 12-month maximum build time frame. According to an attorney in South Africa the contract was in default. He also added that if we would like to pursue this matter legally, he could not represent us because he had already represented Celtic Yachts / Tim Duncan in a similar matter previously. How illuminating!
So we could continue to disrupt our lives and idly sit by waiting for the builder to finish, or we could cut our losses and move on.
Stay tuned for what happens next as we contemplate cutting our losses and ending our dream.
Comments